Is Central Plastic Resin Drying Right For Me? Understanding The Difference Between Press-Side & Centralized Systems
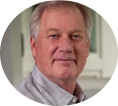
Mark Haynie
June 6, 2023 | 5 min read
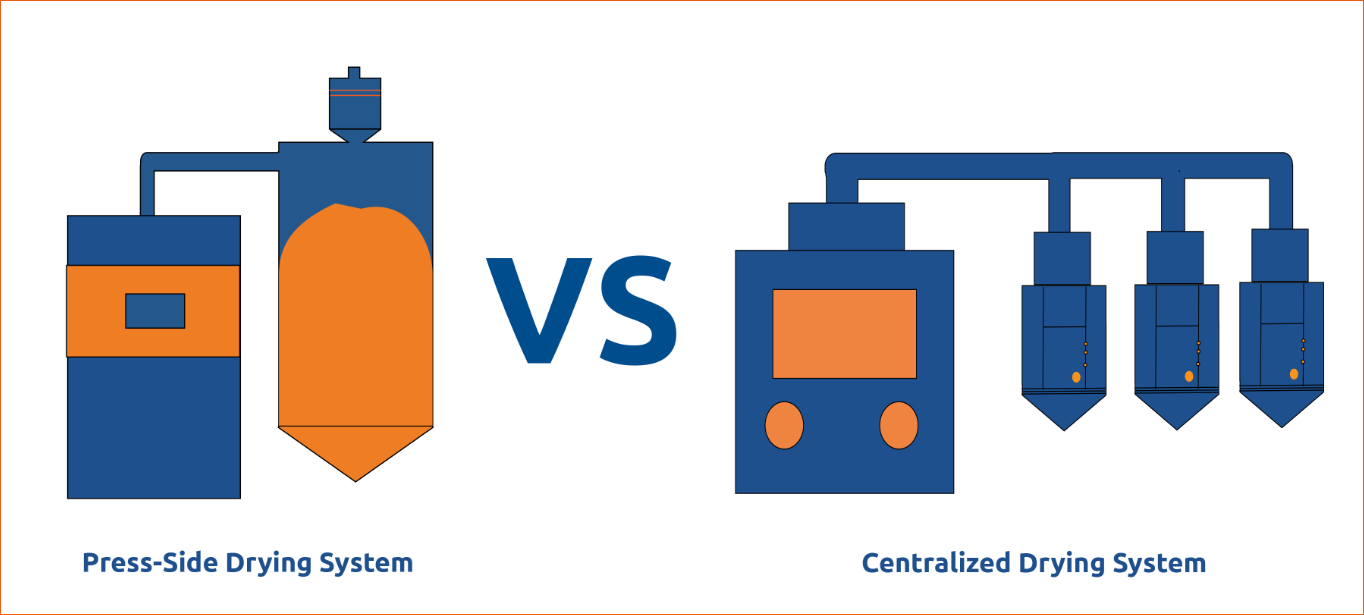
As a plastics processor, selecting the right resin drying system is crucial to ensuring efficient production and high-quality finished products. While press-side resin dryers have been the go-to option for many processors with small-scale operations, more and more manufacturers are transitioning to centralized drying systems to meet their production requirements.
In this article, we’ll explore the differences between press-side and central resin drying systems, the benefits of each approach, and ultimately, why transitioning to a central plastic resin drying system might be the smart choice, especially if you’re looking to increase production, efficiency, and profitability.
Press-Side Resin Drying: When Is It The Right Choice?
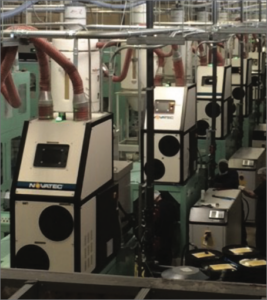
Press-side or press-mounted resin dryers are commonly used in facilities with fewer than 10 process machines and low throughputs (between 25 – 100 lb/hr). This approach is ideal for processors who run the same material on the same machine daily, with minimal material changes.
With press-side drying, there is a vacuum loader at each drying hopper, and a bulk box or drum of resin is the source of material. While this approach is ideal for many processors, it can present some disadvantages for others. For example, this arrangement requires constant forklift traffic and room to deliver material to the presses, which can lead to contamination and wasted materials.
Portable dry/convey units are an interim solution for processors looking to upgrade their drying systems without making the leap to central drying. These units have throughputs of up to 200 lb./hr. and are typically mounted on a cart with a drying hopper, a loader or receiver to supply resin to the drying hopper, and a machine-mount loader or receiver to deliver material to the machine throat up to 200pph.
However, the need for bulk boxes and forklifts remains, which can cause confusion on the production floor and result in materials being left in the bulk bins and/or contaminated and wasted.
Central Plastic Resin Drying: What Is a Centralized System?
Centralized resin drying systems provide a single dryer that can provide -40°dew point air to multiple material hoppers of different sizes. An adjustable heater and blower are mounted on each hopper so the heat and air flow can be adjusted to the material in that hopper. This arrangement allows for custom drying of multiple materials from a single central dryer that is sized to match the requirements of the bank of hoppers.
Central plastic pellet dryers are available with throughputs from <200 lb/hr through 5,000 lb/hr, which meet a wide range of processor needs. Processors often have more than one central dryer – each serving a bank of hoppers with a back-up central dryer for times when a dryer may be taken offline for maintenance.
Are You a Good Candidate for Central Drying/Conveying?
If you have dryers on 10 or more machines, a single material that requires drying at multiple machines, frequent material changes on your machines, or use more material types than you have machines, then central drying is most likely the best option for you.
Additionally, centralized resin drying offers a notable advantage: the ability to pre-dry the next resin, thus curtailing non-productive time. By establishing a network that interconnects various processing machines with a centralized drying unit, processors can seamlessly sustain production while simultaneously preparing the subsequent resin for deployment.
This eliminates the waiting game, slashes changeover durations, and ensures optimal drying conditions for different resin variants. The outcome? A substantial boost in productivity, minimized downtime, and a surge in operational efficiency.
Centralized resin drying systems also provide flexibility to serve the needs of your customers, reduce operating costs, and improve worker safety. If you have a justin-time objective to reduce inventory, need to reduce operating costs, or want to expand without sufficient space, then a centralized resin drying system is the perfect solution for your operation.
The Benefits of Central Resin Drying
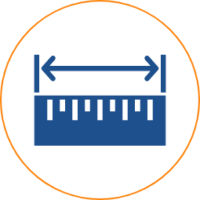
Space Savings:

Consistent Quality
Energy Savings
Reduced Labor Costs
Improved Material Handling
Increased Efficiency
Cost Savings with Centralized Drying
In addition to the benefits listed above, a centralized drying system can also provide significant cost savings. Let’s consider a scenario where a processor has 12 machines in a plant, each with its own individual dryer with an average throughput of 200pph drying Nylon/ABS/PC material. Assuming an average energy cost of $0.10 per kilowa-hour, the energy costs for that Press-Side operation could equal up to $108,000 per year, but with a Central Drying System would only amount to $41,000 per year.
Now let’s look at that same 12 machine plant scenario when it comes to material changes. Press-side dryers require 30 minutes to 4 or 5 hours for material changeover, but a Centralized System can reduce material change times to approximately 15 minutes by allowing you to pre-dry the next resin. So, let’s base the Press-Side equation on a 2-hour average with 3 changes per machine each week. The costs for Press-Side material changes could equal up to $180,000 annually but at an average of 15 minutes per change with a Centralized System it only amounts to $22,500 annually. That’s a huge difference!
Lastly, let’s examine labor costs. A Centralized System will typically eliminate at least one material handler per 12 machines. That’s at least a savings of $30,000 annually. When you add up all of these costs, the Press-Side operation for the 12-machine plant equals $318,000 per year while the Centralized System for this type of plant would only total $63,500 per year. That’s a savings of $254,500 per year with a Centralized Drying System…EVERY YEAR!
What about the material that is lost per bulk box? If we assume that 10lbs of material is lost, that equates to anywhere from $13,000 – $43,000 per year depending on the material. And how about the wrong material being processed? Has that happened at your plant? Add clean-up, disposal, and lost machine time and you can easily triple these costs.
Increased Floor Space Means More Room for Production
Is your manufacturing area getting cramped and overcrowded? When using pressside dryers, you’ll typically need to allow an extra 75 sq.ft. per process machine for a dryer, hopper, and bulk box. Now if you add the space needed for a forklift to maneuver in, as well as room to haul away old bulk boxes and replace them with new ones, you’re suddenly up to 120 sq.ft.! Multiply that by the number of presses you have and you’ll see how many additional presses you can fit into that space – that, after all, is supposed to be your manufacturing area – where profits are made. That valuable floor space could be used to add more production machines. PressSide operations can cause your manufacturing area to become a crowded and inefficient space but switching to a Central Drying System can free up the valuable space needed to make more parts each day and increase your profits.
The Novatec Difference
While press-side resin dryers may work for some processors with fewer than 10 process machines and low throughputs, more and more processors are converting to centralized drying systems due to their production requirements and economic advantages. A centralized drying system provides numerous benefits, including space savings, consistent quality, energy savings, reduced labor costs, improved material handling, and increased efficiency. Additionally, a centralized drying system can provide significant cost savings, particularly for larger processors with multiple machines and dryers. If you’re a processor with 10 or more machines, frequent material changes, or a need to reduce operating costs, a central plastic resin drying system is the perfect solution for you.
But when it comes to choosing a drying system for your plastics manufacturing operation, the decision is not one to be taken lightly. The quality of your drying system can directly impact the quality of your finished products, as well as the efficiency of your production process as a whole. That’s why Novatec is proud to offer the most advanced and reliable central drying systems on the market today.
With over 75 years of experience as the longest-running manufacturer in the business, Novatec has built a reputation for unparalleled quality and reliability. Our team of Centralized Systems Experts are committed to client success and provide full-time professional project management staff, ensuring that each and every project is executed to perfection.
The Ultimate in Streamlined Efficiency
When you switch to a Novatec central drying system, you’ll enjoy the ultimate in streamlined efficiency, helping you save valuable floor space and add more production machines. This means you can achieve your number one goal: making more parts each day.
Don’t settle for a subpar drying system that may cause inefficiencies and impact the quality of your products. Choose Novatec and experience the peace of mind that comes with working with the number one industry leader. Learn more here.
Mark Haynie
Novatec
Vice President
Moisture & Drying Technology
Mark has been designing and installing dryer systems for over 40 years and has worked at Novatec, a leading dryer equipment supplier for the plastics industry, for 25 years. Mark is a well-known and well-respected resin drying expert. Throughout his career, Mark has visited thousands of plastics plants offering solutions for drying challenges and has authored many technical drying and moisture-related articles.