Gas-Fired Process Heaters
The operation of a gas-fired process heater involves burning natural gas or propane in a combustion chamber to produce heat, which is then transferred to the plastic resin or product. The heater can be designed in various configurations depending on the specific application and the heating requirements. For example, a heater may have a vertical or horizontal configuration, and may use a direct or indirect heating method.
Gas-fired process heaters are commonly used in the plastics industry because they can provide fast and efficient heating, allowing for high throughput and productivity. Additionally, they can be used for a variety of plastics processing applications, from melting plastic resin to curing finished products.
Gas-fired process heaters can be designed with various safety features, such as automatic shut-off valves and flame sensors, to ensure safe operation. They are typically made of durable materials, such as stainless steel, to withstand the high temperatures and harsh conditions found in industrial environments.
In many parts of the country, using natural gas instead of electricity can significantly reduce energy costs. Besides reducing costs, there are often programs that provide energy credits to companies that reduce energy usage – so there can be a double benefit in switching to gas.
The key to maximizing benefits is choosing a gas-fired process heater that has the highest energy-efficiency possible. Most gas-fired heaters have an efficiency rating of only 75-85% but there are models with 90+% efficiency ratings.
Types of Resin Drying Systems
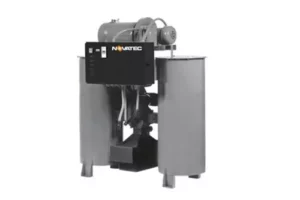
Silo Dehumidification/ Hot Air Dryers
What is a silo dehumidifier and how does it work and compare with other resin drying systems?
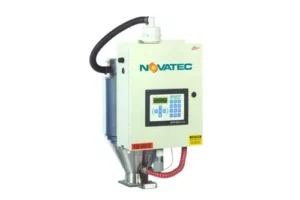
The principle of compressing air in factories for power tools and other high-pressure uses has a side benefit for the world of resin drying.
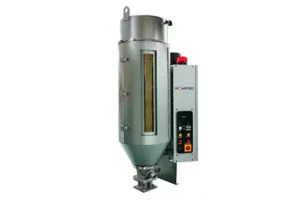
What is a membrane resin dryer and how does it compare to a compressed air dryer without a membrane?
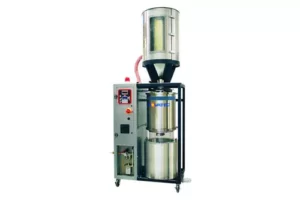
What is a vacuum resin dryer and how does it draw moisture away from plastic pellets in vacuum processing?
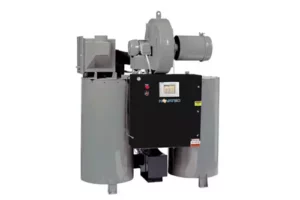
Dual Bed (also called Twin Tower) dryers used to be the most commonly purchased type of resin dryer. A look at why, and where the technology has progressed.
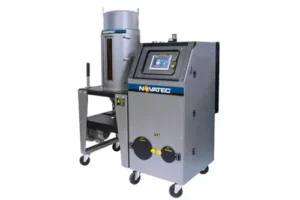
The advantages of desiccant wheel dryers include operating at a low temperature, which is important for preventing thermal degradation of the resin.
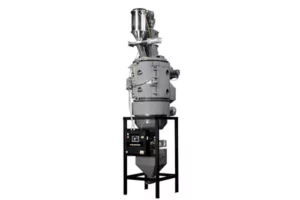
Technically, crystallizers are not dryers. They are used to convert PET from an amorphous, back to a crystalline state for re-processing.
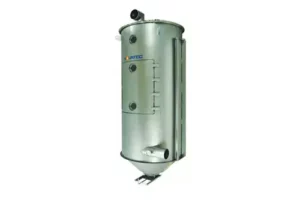
Drying Hoppers for Plastic Resins
Drying hoppers are part of most drying systems. At a glance, they look much the same, but there are certain features you should look for.
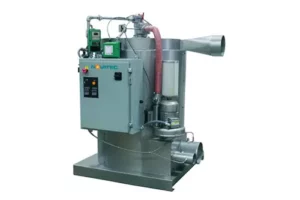
What are the benefits of gas-fired process heaters for drying plastic resins?
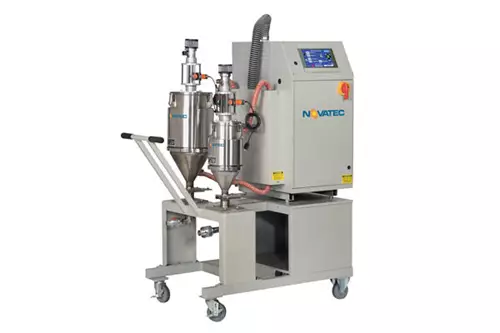
Resin drying machines that can be moved from machine to machine within a plastics processing plant have advantages and disadvantages over a central drying system.
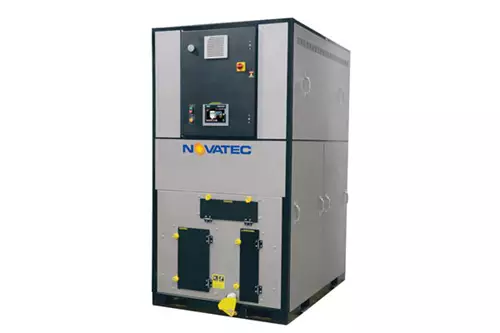
Properly designed Central Drying Assemblies are easily connected together to save installation costs.
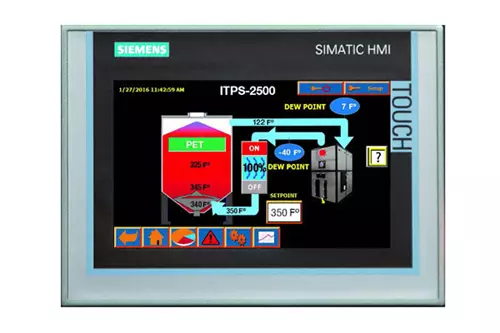
PET Energy-Saving Drying Systems
Learn about the keys to drying PET efficiently while saving space and energy.
Ask the Expert
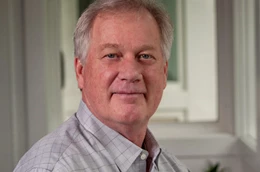